ARTICLE SUMMARY
Business process modeling is essential for understanding and improving operations. Learn how you can implement it to make your business more efficient.
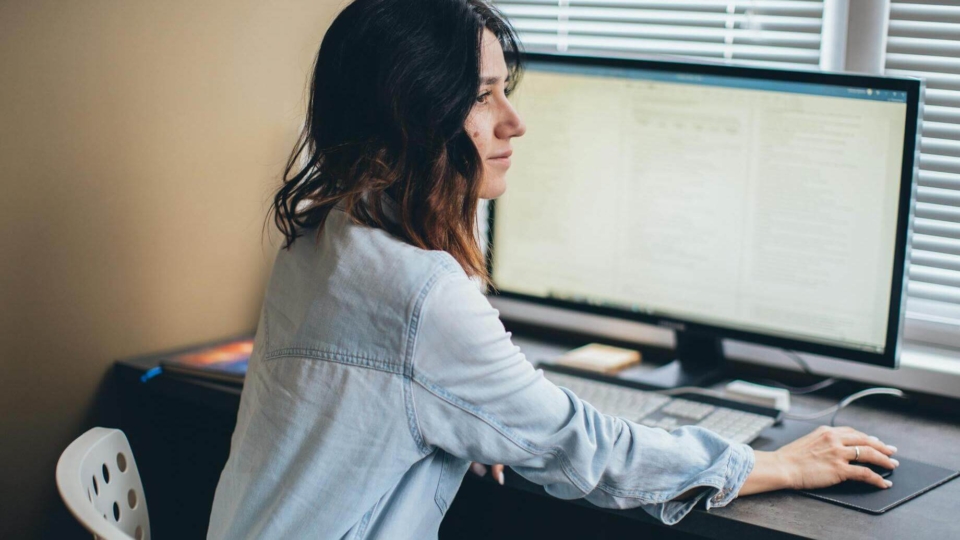
Your organization’s day-to-day operations rely on a variety of processes, but do you really understand them? Keeping track of each step in the process and the connections between them without visual aids is a daunting task. That’s where business process modeling comes in.
By allowing you to visualize entire processes from start to finish, business process modeling serves as an invaluable tool for analyzing and improving business processes at every scale.
Build smarter, more agile processes with our workflow management crash course
What is business process modeling?
Business process modeling is the practice of representing business processes in visual form. These models often take the form of flowcharts or workflow diagrams that display all the steps in a process and how they are related.
Business process modeling is a key step in implementing a business process management (BPM) strategy. BPM is an organization-wide practice that requires modeling, analyzing, and optimizing business processes, with the goal of improving efficiency and effectiveness. Increasingly, companies are investing in low-code BPM strategies.
The modeling component of BPM allows business managers to visually break down these processes and better understand how they’re operating. This involves both the current state of processes — the “as-is” processes — and the ideal future state of processes — the “to-be” processes.
A dedicated BPM platform can be invaluable in creating and optimizing business process models. For instance, user tagging and alerting can help speed up the triaging and hand-over times between process steps, and historical data can be used to make smarter decisions about how to improve models in the future.
The business process model defines the steps that comprise the process, clarifies who is responsible for performing them, shows any possible variations in the process, indicates the expected duration and importance of each step, and so on. By tracking and monitoring the performance of each stage of the model, you can better determine where inefficiencies may lie and start developing new to-be processes that can minimize issues.
For example, customer onboarding is an important, complex process that benefits from building a visual model. You want to make sure that the unique needs of each customer are met while they’re onboarded, which requires a process that branches out and features multiple variations. Without mapping out these branches, your team members will likely fail to keep track of such a complex process, and customers will be left confused and dissatisfied.
Or take expense reimbursement, another process many businesses employ daily. Employees want to know exactly what they need to do when submitting requests and what stages the request will go through before they are reimbursed. Building and sharing a process model makes all team members aware of how expense reimbursement is handled and will reduce frustration among employees and the reviewers in HR.
Why is process modeling important?
Business process modeling is a physical representation of process activities and provides a holistic view of processes. It also provides a more granular understanding of the specific steps involved. To better understand the importance of business process modeling, consider these benefits:
Gain process visibility
By listing and detailing all events, actions, and connection points that exist between Point A (the action that sets your process in motion) and Point B (the overall result of your process), it becomes much easier to identify redundancies, unnecessary steps, and performance bottlenecks. These benefits apply to all parts of your business, from customer service to accounting to sales.
Create process alignment
Business process modeling also removes any ambiguity regarding what steps to follow when performing a process. All team members know their responsibilities and exactly what their roles are. This keeps your employees aligned and facilitates improved communication and collaboration.
Improve employee productivity
As noted above, business process modeling is also a critical part of practicing BPM. Without visualizing your organization’s processes, it’s impossible to accurately diagnose issues and decide on improvements that make sense. By optimizing the processes your business runs on, BPM makes each employee more productive and ultimately improves the bottom line.
Techniques for business process modeling
There are many methods for producing business process models. Three of the most popular are Business Process Model and Notation, process flowcharts, and Universal Process Notation.
Business Process Model and Notation (BPMN)
Business Process Model and Notation (BPMN) is a standard methodology for the graphical representation of business processes. It defines different elements such as events, activities, and connections. BPMN allows different stakeholders within a business to standardize their language when describing and analyzing processes. It does require team members to familiarize themselves with its nomenclature, which creates more of a learning curve than other available techniques.
BPMN benefits
- Graphical representation of a business process
- Commonly designed as a flowchart
- Supports better process management for technical users and business units
- Adopts a common language and provides a standard notation that is understood by all stakeholders, including business analysts, developers, and managers
Process flowcharts
Process flowchart benefits
- Graphical representation of a business process
- Provides a top-down understanding of how a process works and the steps that makeup the workflow
- Ideal for improving or standardizing processes
- Also used to model and create a standard operating procedure
Transformational process modeling
Transformation Process Modeling is defined by a series of input-output relations that ultimately lead to the final process. With this model, each process is divided into actions usually referred to as either steps or activities. They then are divided again into sub-actions and each of them has inputs that are transformed into outputs, creating a logical work sequence.
Transformational process modeling benefits
- Graphical representation of a business process
- Made up of six elements: inputs (what’s needed to provide service or product), transformation process (actions needed to solve input needs), outputs (how transformation processes affect inputs), customers (recipients of product or service), and feedback loop (opportunity to judge work)
- Typically used to outline the processes involved in producing a product or providing a service
- Ideal for process improvement modeling
Universal Process Notation (UPN)
UPN is an alternative to BPMN that attempts to make processes more visually compact and allow any type of user to understand them. The basic component of UPN defines the following question words: When, What, Why, How, and Who. This makes it clear exactly what the intent of each step is and who is responsible for them.
UPN benefits
- Graphical representation of a business process
- Less complex than BPMN because it maps processes with five standardized building blocks: who is involved, what happens, when does it happen, why does it happen, and how does it work
Hierarchical process models
Unlike more traditional business process modeling techniques that work in a linear manner, this model uses process trees. To help visualize this, consider an actual tree’s trunk and branches.
The process tree represents the process itself, the branches represent the flow of tasks, and the leaves represent the tasks within the workflow. Because of its build, this technique works best with complementary modeling techniques, so as to better connect related processes and define correlating tasks, and subtasks.
When do I need business process modeling software?
Deciding when to leverage business process modeling software isn’t an exact science, but there are some telltale signs like:
Process modeling software can be helpful if you need visibility into process details like:
- Decision/approval points.
- Tools, apps, or software involved in the process.
- Who owns or initiates those events and activities.
- Different paths workflows can take based on their outcomes.
- Tasks, steps, events, and handoffs that occur within a workflow.
By understanding these elements, it will become much easier to measure process success and failure rates and the steps that can be taken to increase success and lower failures.
What are the five steps in process modeling?
How you create a business process model depends in part on which of the techniques above you use, but each approach will involve the same general steps once you’ve identified the process you want to model. Below are the five necessary steps to get started.
1. Define the improvements you want to make
The point of process modeling is to find ways to improve processes. But in order to make things better, you first have to define the improvements you want to see. Higher productivity, less delays, faster approvals, better work handoffs — these are all examples of improvements that can be modeled and implemented.
2. Take inventory of existing processes
Once you know what you don’t want, it’s time to start working on what you do want. Before process modeling begins, you should review relevant data and interview those who use the process every day before modeling it in its current state.
Whether you use a modeling software or process management platform, map the process or processes you’re interested in improving. It’s recommended to start slow and then scale in order to ensure that each process is mapped properly. People, tools, tasks, workflows, steps — take inventory of everything that makes a process run from the process start trigger to the endpoint and outcome, including the little messy details like workarounds and shadow IT.
Once you’ve carefully evaluated the as-is process, the problems you identified earlier (and the solutions) will be much clearer.
3. Model the to-be process
Once you understand what needs to be improved, it’s time to model the updated process. After creating the model, run it by the key stakeholders to see what they think and incorporate any useful suggestions they have.
It’s important to document every step of the improvement process — from start to finish, including every interaction, handoff, connection, and tool — so that there is a record you can refer back to. This will also make it easier to manage and communicate the changes that are being made and fine tune the improvements.
To ensure documentation is useful, follow best practices like:
- Keeping a logical and clear sequence in your diagrams.
- Defining a naming convention for your process models.
- Keeping your processes as simple as possible.
In addition to modeling the process, this is the time to define the amount of time you want to run the improved process. To get an accurate read of the changes, consider waiting 3-4 weeks before revisiting the process and making updates.
4. Deploy and test
Once the improved process has been modeled and stakeholder feedback has been implemented, it’s time to roll out the changes. The important thing to keep in mind at this stage is communication. Changes are uncomfortable (especially for teams that have grown accustomed to running a process a particular way), so over-communicating the changes being made, why they’re needed, and how they’ll improve day-to-day work and outcomes is essential to a successful rollout.
5. Monitor and update on a regular basis
After letting the improved process run for the appropriate time, it’s time to revisit the improvements and determine whether the changes are helping or whether they need to be workshopped more. Sometimes what’s mapped may not actually perform as expected, so it’s important to connect with the people who are involved with the process to understand how it’s truly performing, in addition to looking at performance metrics.
Make it a continuous practice to revisit the process to ensure that it continues to provide value.
Best practices for process modeling
It’s important to structure your models in a way that’s useful and understandable for everyone involved in the processes. There are a few best practices you can implement to do so.
Avoid making the model overly complex
While you may be tempted to try to map out every possible step and outcome, this can lead to models that are hard to understand due to their excessive scope. When possible, try to be compact and remove any redundancies.
Plan the steps ahead of time
In other words, don’t just dive right into building the model. You’ll want to discuss the plans with all process stakeholders to make sure the information is correct and makes sense to them. Otherwise, you risk an incorrect or over-complicated model as you start to modify it in response to feedback.
Keep in mind that the goal is process improvement
You should structure the model as an aid in detecting inefficiencies. The scope of steps should be wide enough to encompass useful information but narrow enough to locate specific issues. You may have to iterate on the model to find the optimal balance.
What are examples of using process modeling in organizations?
To further illustrate the benefits and uses of process modeling, here are some examples of the positive results process modeling can create for organizations.
Berneck
As the company grew, the team in charge of exports needed a scalable solution to replace a costly and inefficient legacy system that hindered scaling and made tracking orders and lead times via Excel nearly impossible.
As operations continued to scale, it became clear that managing orders with the existing process management methods was not sustainable. The team also struggled with measuring and tracking the booking process because they didn’t know exactly where to find the information they needed due to the booking operation’s manual management via email communications.
By using a no-code process automation and management platform, the team significantly cut costs and is now saving thousands a year by preventing late fees with SLA tracking and automatic deadline notifications. Today, processes are standardized and optimized, team morale is up, information is seamlessly shared between teams and orders are easily tracked.
Keep reading: Learn how Brazil’s largest wood exporter gained control of inflating costs and reduced lead time by 31%.
Capgemini
Capgemini Brazil’s HR department received an average of 2,500 requests per month through many channels like email, direct messages, and verbal requests without any categorization or prioritization. This legacy process also had pre-existing bottlenecks that negatively affected their employee’s experiences. A process analysis revealed several opportunities for improvement to Capgemini’s HR leaders.
After identifying the main bottlenecks and pains of their employees, Capgemini’s HR department started the second step of the project: mapping the 95 types of requests, like medical leave, benefits management, recruitment, training, and offboarding. They aimed to standardize all processes, from request opening to delivery (before even thinking about implementing automation).
After mapping their new and improved processes, launching their “Talk to HR” portal, and adopting a process automation platform, the Capgemini team was able to:
- Centralize all requests in a single portal and moved from manual work to now focus on value-added activities and more complex requests.
- Lower costs by streamlining work that previously took 5 employees to complete down to only 1.5 full-time employees.
- Improve the ability to measure each step of the process so managers can continuously improve the workflows to achieve even better results.
Keep reading: Learn how Capgemini Brazil improved their monthly HR request SLA achievement from 38% to a monthly average of 98% achievement.
Business process modeling tools
Companies leverage BPM tools in order to assess their existing processes and to build better, more efficient versions of those processes. BPM tools can be used to model, automate, and orchestrate any of the different types of business processes. In addition to conventional BPM software, businesses today have alternatives that can meet many of the same needs.
One of the most powerful alternatives to traditional BPM tools available is no-/low-code automation (NCLC) software. NCLC tools give business users a visual interface that allows them to quickly and easily model their processes, customize workflows, and automate tasks. NCLC tools also help IT teams by providing a secure set of tools so that business users don’t have to send every change request to the IT backlog.
Process automation also helps business teams stay agile by allowing them to model, modify, and monitor their processes in real-time, responding to competitor activity, customer feedback, or internal requirements.