ARTICLE SUMMARY
In the Lean Management world, Gemba Walk is one of the most relevant and essential concepts. This Japanese word can be translated as “the place where things happen.” You’ve probably walked through the Gemba before, or you might have even worked on it without realizing it. Whatever the case, going to the Gemba has to be something natural for any professional that has Lean as their major work philosophy.
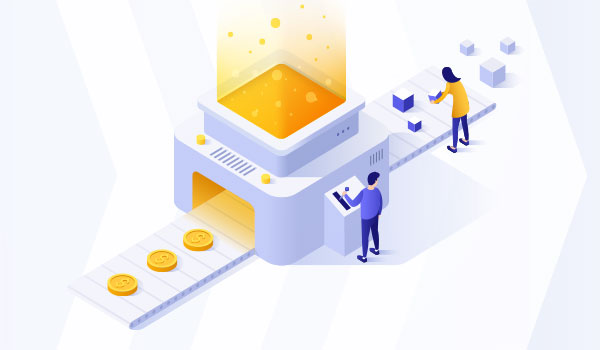
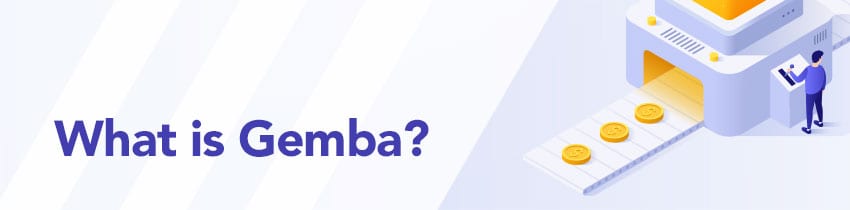
In the Lean Management world, Gemba Walk is one of the most relevant and essential concepts. This Japanese word can be translated as the actual place or the place where things happen. It can take shape in a lot of contexts, such as the office of an accounting company, the kitchen of a restaurant or the shop floor of a factory. This is the place where value is generated, regardless of the industry we’re talking about. Be prepared to walk through the Gemba after reading this article.
But first, if you want to learn more about Lean before continue reading this content, check out our Beginner’s Guide and our Lean Glossary.
Let’s go to the Gemba!
You’ve probably walked through the Gemba before, or you might have even worked on it without realizing it. If you think of a manufactory, Gemba is the shop floor. But if you work on a SaaS company, Gemba is the Tech team’s floor. In other words, Gemba is where actions that generate value take place.
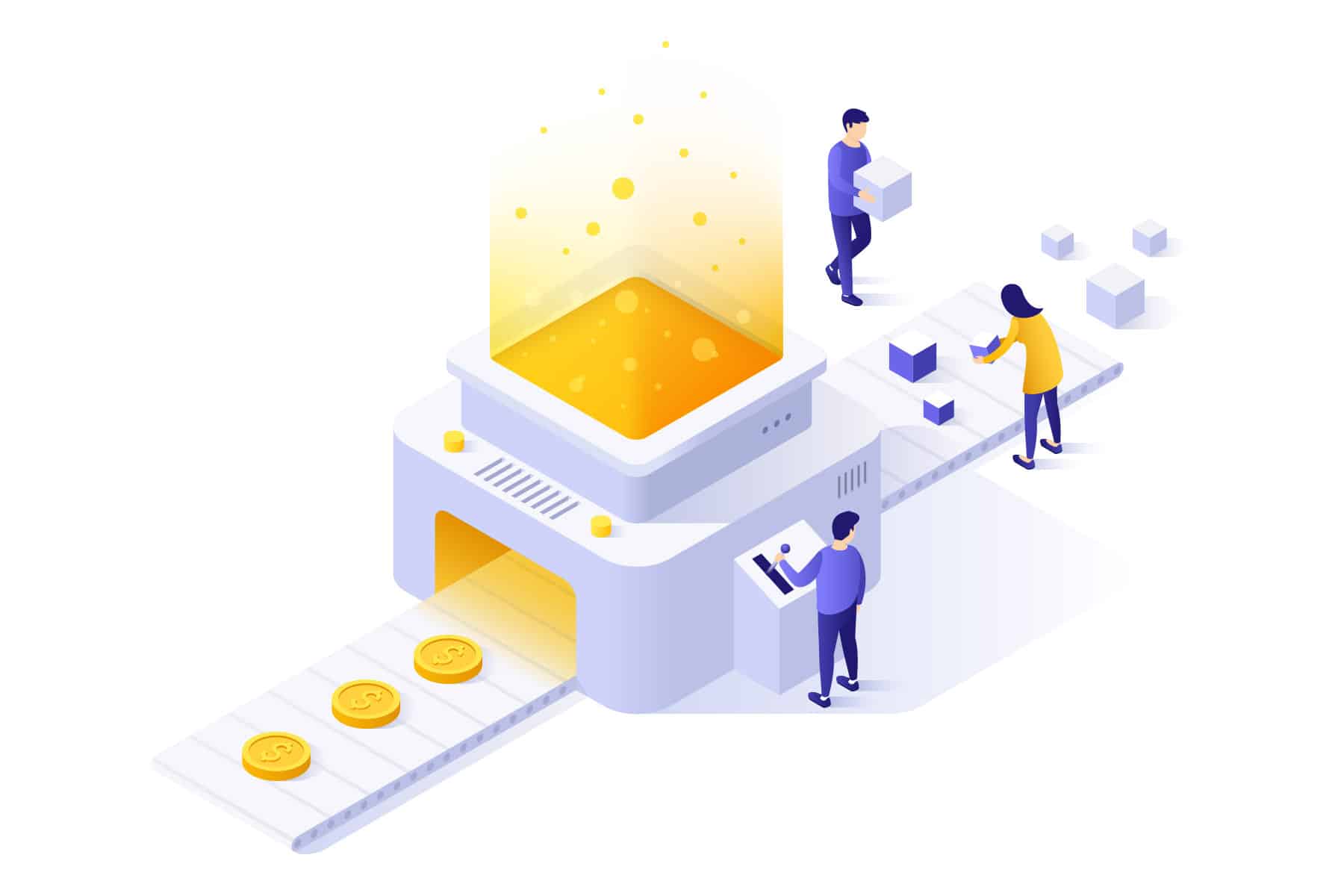
Whatever the case, going to the Gemba has to be something natural for any professional that has Lean as their major work philosophy.
Get people involved
When you have a deeper engagement with the employees working at the Gemba, you begin to fully understand the root causes of many problems that may be occurring in your company. In Lean terms, you really shouldn’t be sitting on your chair all day. Instead, you should be talking to those who are on the front line of your company’s processes.
By examining the flow of the process in the actual place, it’s possible to see how the process usually works, what happens when obstacles come your way, what types of issues arise and how they are solved. Also, the difference between what’s written on paper and what really happens at the Gemba becomes crystal clear.
That’s why it’s so crucial to do a Gemba Walk. Being there in person and getting to talk to the people, examine their work up close, ask questions and learn from their daily struggles—always showing respect (that’s essential in any Gemba Walk)—is a priceless experience for the business. Keep in mind that this is a chance for managers and leaders to get hands-on to identify wasteful activities and improvement opportunities.
Ask the right questions
So you can make more accurate and precise improvements, it’s important to go prepared to the Gemba and ask the right questions. Here are some good examples:
- What are you doing? Why do you do it this way?
- What challenges do you face on a daily basis?
- What can or can’t you solve in your role?
- What tools do you use to manage tasks?
- Who do you talk to when facing trouble?
- What do you do when things go wrong?
- What kind of waste do you see here?
Of course, these questions will change according to the context and operation to be analyzed (although this is a good start for a Gemba Walk). But before you begin the walk itself, know that you should keep an eye on the processes and not evaluate the people, but their tasks:
Build a strong team
It’s desirable to take a diverse team with you during the walk to have different insights and ideas. Also, validate any assumptions you may have with the people in the process—do not rely on guesses.
Review your notes
Make sure you write down everything you see in the walk and analyze it afterward. It may include things like problems to solve and tasks to be completed. Keep in mind that the goal here is to boost the entire process, make it easier, safer, more clever and faster (to sum up, better).
Take the best out of it
Gemba Walks result in better communication between teams and in positive changes for the entire organization. Truth must be told: this is a simple yet effective activity because, by visiting the Gemba, you can make a reliable diagnosis of the process. After that, Lean concepts and tools, such as the Value Stream Mapping and A3, will help you find solutions for the problems detected in these walks and talks.
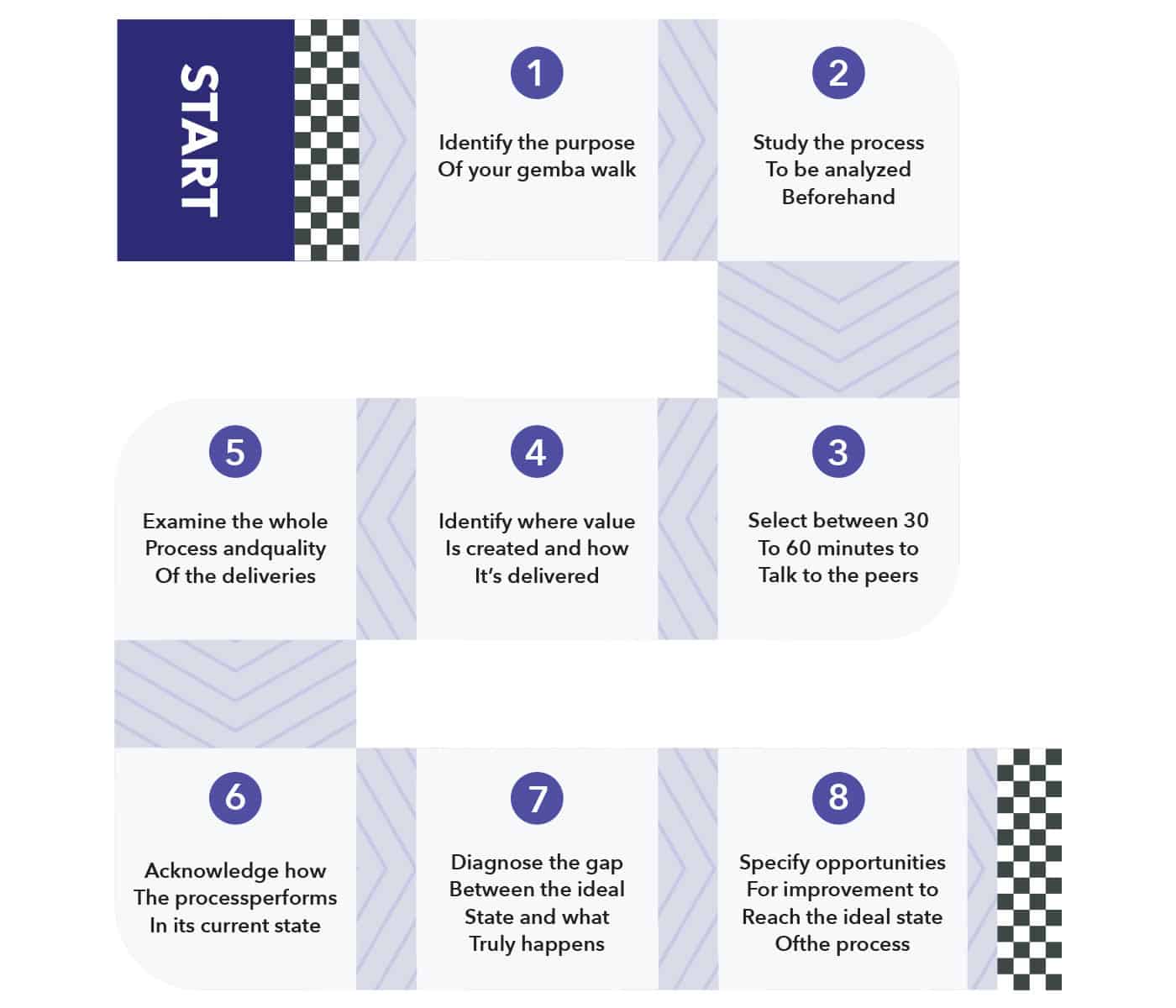
True improvements can only be made when everyone is on the same page, especially if we’re talking about cultural changes and not just minor updates in some processes. That’s Kaizen, the continuous improvement philosophy that focuses on the big picture and not just on a single thing, a philosophy that is deeply related to the Lean mindset.