ARTICLE SUMMARY
The Lean universe is filled with expressions, acronyms, foreign words and concepts that don’t seem easy to understand at first. Checkout our glossary.
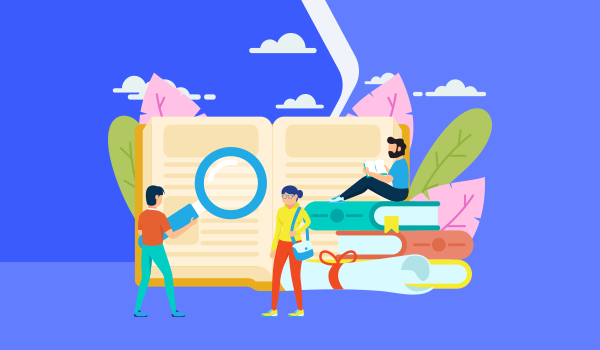
The Lean universe is filled with expressions, acronyms, foreign words and concepts that don’t seem easy to understand at first sight. However, we’ll show you in this glossary that the vocabulary is much simpler than you thought—you just have to get used to it!
Keep in mind that this is a complementary material that you can revisit whenever you want to (a quick guide with the essentials terms). We strongly recommend you to read the Beginners Guide for Future Lean Experts if you want to dive even further into theories of Lean. In that guide, you can learn in detail most of the terms presented below in an easy and light way.
This glossary was created to simplify ideas and translate them into a few words. If you want to know more about what is shown here, don’t forget to keep up with our blog and newsletter. Lean has a language of its own, learn how to speak it!
The best Lean content is one click away! Subscribe for more!
3 Ms: The 3 Ms stands for Muda, Mura and Muri. They represent waste, overburden and unevenness, respectively. In order to achieve better flow, the 3 M’s must be neutralized.
5 Ss: Sort, Set In Order, Shine, Standardize and Sustain. The 5 Ss create and maintain an intuitive workspace. It’s all about a great environment for the employees and the company.
5 Whys: The 5 Whys technique consists of questioning yourself or your team five times or more of why a problem or defect happens until you reach the root cause.
7 Wastes: Transport, Inventory, Motion, Waiting, Overprocessing, Overproduction and Defects. The 7 Wastes are the villains of any process and must be reduced to the maximum.
A3: An A3 consists of a large piece of paper in which the person draws the current state and the future state of the company. It’s a great tool for planning, problem-solving and status reporting.
Andon: Calling attention to defects or abnormalities of the flow in order to stop the process until what is wrong is identified. The concept comes from the Andon Cord of conveyor systems.
Bottleneck: Anything that steps in the way to block the flow of the processes, allowing problems to arise and compromising the continuity of the stream.
DMAIC: Define, Measure, Analyze, Improve and Control. This is one of the main concepts of Six Sigma methodology and resonates within Lean as well.
Flow: The state of a process in which the parts move from one step to the other in a steady, continuous stream without compromising quality.
Gemba: The place where the work happens and the product is made (it can be an office or an industry). It comes from the Japanese word Gemba, which literally translates to the real place.
Genchi Genbutsu: A concept that is directly attached to the Gemba. Genchi Genbutsu means go check and see for yourself, go to the Gemba to see how things are working.
Heijunka: A production leveling process that sets a limited period of time due to demand. This prevents overstocking, reduces costs, work energy and lead time throughout the value stream.
Hoshin Kanri: It is a methodology of strategic planning and management of processes, also known as policy deployment. Here you’ll lay the groundwork for the execution phase.
Jidoka: The automation with a human touch. It represents processes automation that only demands a human interaction when a defect occurs or when exceptions must be handled.
Just-In-Time: Methodology in which production is only activated when there’s a demand for it. One of the cores of Lean directly attached to ideas such as Pull System and Heijunka.
Kaizen: It can be translated from Japanese as Continuous Improvement. It is the main philosophy of Lean in which you seek to be better each day.
Kanban: A type of visualization flow designed by columns and cards in which everyone can follow the progress of the processes, know who is doing what and what still has to be done.
Lean: A set of techniques and methodologies that strives for waste avoidance, quality boost and continuous improvement in all processes, regardless of the field of the company.
Muda: One of the 3 Ms, Muda represents waste in all forms, such as waste of time, labor, resources and money. This is one of the biggest enemies of Lean and must be avoided.
Mura: One of the 3 Ms, Muri represents unevenness, variation and irregularity. It stands for any activity, task, process or person that is not steady.
Muri: One of the 3 Ms, Mura represents overburden. It can be interpreted in different ways, such as when someone in a team has a huge amount of work while the rest is otiose.
PDCA: Plan, Do, Check and Act. A four-step management method used to control and improve processes and products of any kind. Usually applied together with DMAIC.
Poka-Yoke: Any mistake-proof mechanism created to prevent processes from becoming bottlenecks. It can be seen as error detection and prevention as to not disturb the flow.
Pull System: A flow planning system that takes demand into account to begin the production only when needed (avoiding waste, reaching precision and adopting a higher adaptation).
Root Causes: The core reason that causes the problems of a process below the surface. Often overlooked for minor issues, one of the ways to reach the root causes is through 5S.
RPA: Robotic Process Automation is the use of software with artificial intelligence and machine learning capabilities to perform human activities or help humans in ordinary, repetitive tasks.
SIPOC: Suppliers, Inputs, Process, Outputs and Customers. SIPOC is a tool that summarizes the inputs and outputs of one or more processes represented by diagrams.
Six Sigma: In a few words, it’s a set of management techniques to improve business processes by reducing the probability of errors or defects. It’s directly connected to the DMAIC system.
Takt Time: The average amount of time between the beginning of one activity until the start of the next. The word takt comes from German and means rhythm.
Toyota Manufacturing System (TPS): The TPS was the system developed in Toyota in the 40s and it’s the earliest version of Lean. The majority of the Lean principles emerged from here.
True North: An expression used to define the organization’s goal from the current condition to where they want to be. It can be seen as a strategic plan or a mission statement.
Value: Everything your customer is willing to pay for. The product or service that you provide to the market and how your customers are seeing it.
Value Stream Map: A major flow visualization of all the steps required to deliver a product or service. It’s the design of the current state of the company and the future state to be achieved.
Yokoten: It can be translated as horizontal deployment and it’s all about sharing good results and examples of Kaizen from one area of a company to another.
The Best Lean Management Platform!