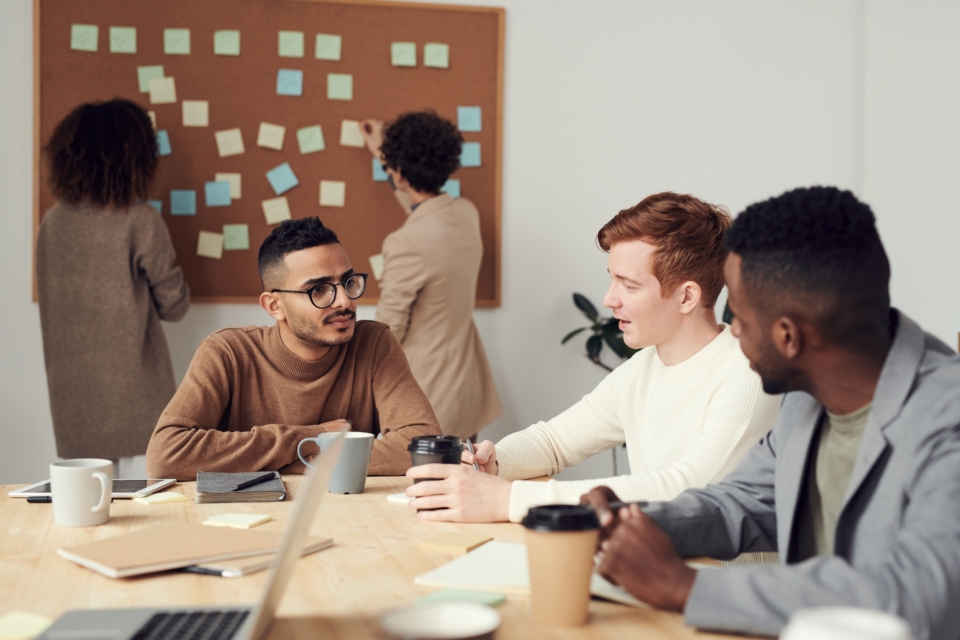
A common pitfall that occurs when creating or updating business processes is the failure to revisit or update them. Many businesses may even continue using them the same way long after they’ve been created or updated simply because they’ve always done it that way.
However, this mindset leads to a lot of waste, as conditions, people, and resources change over the years. Some tasks may become redundant, while others are unnecessarily repeated, wasting both time and materials.
Efficiency is crucial for remaining competitive, which is the primary goal of lean process improvement. This guide shows how implementing this approach can transform your business by taking it to new heights of efficiency.
Learn how to do more with less with the Definitive Guide to Business Process Automation
What is lean process improvement?
Lean process improvement is a methodology for reducing the time needed to fulfill an order. Toyota originally developed it for manufacturing, but lean process improvement is also used in many other environments, like government, healthcare, services, and technology.
The idea behind it is that a big-picture view can identify ways to eliminate waste from a process, whether it’s in the form of time, money, or energy. Lean process improvement is a long-term solution that takes time to implement, as it requires an organization to change its culture and mindset.
Assume, for example, that the team members in a marketing department aren’t communicating with each other, causing multiple people to take the same task and leaving other tasks unattended.
This team could benefit from a methodology like lean process improvement because it’s easy to follow and effective at identifying the simplest solution to their problem.
Reading recommendation: The In-Depth Handbook to Business Process Management (BPM)
What are the benefits of lean process improvement?
The benefits of lean process improvement include waste reduction, continuous process improvement, and greater customer focus.
Waste reduction
Businesses typically use many processes to accomplish their goals by maintaining consistency and order. While this method increases efficiency, it can often lead to inefficiency due to the many moving parts and processes. As a result, their performance and oversight often drops over them as business priorities change.
This trend creates waste in the form of delays, redundancies, and costs. Lean process improvement helps teams keep process efficiency a high priority by streamlining processes and only keeping what is absolutely essential.
Continuous improvement
Many companies adopt continuous improvement initiatives. Achieving success in today’s business environment means always looking for ways to do things better, so continuous improvement is a matter of remaining competitive.
Dysfunctional processes can cause many problems such as dissatisfied customers, stressed employees, increased costs, and missed deadlines. As a result, continuous improvement that lean process methodologies provide is a great benefit, especially for organizations with processes that aren’t working well.
Customer focus
Lean process improvement requires companies to maintain a tight focus on business procedures. Eliminating wasteful tasks makes processes easier to implement, use, and maintain.
This benefit also improves the visibility of business operations to stakeholders like customers. In addition, a focus on providing customer value also allows an organization to better predict the customer care it can provide.
5 steps for implementing lean process improvements
Implementing lean process improvement consists of the following steps:
- Identify and map the current process
- Identify problems and eliminate waste
- Establish standardized work procedures
- Implement continuous improvement practices
- Ensure sustainable improvements
Step 1: Identify and map the current process
Defining and visualizing the current process is the first step in implementing process improvement. This step relies on visual elements to represent a workflow, such as cards or a white board.
Text-based methods don’t work well for process improvement because they create a disconnection between the work that a process does and how it does it. Creating a workflow map, such as a flow chart, gives team members a true understanding of the processes by which tasks are completed.
Visualizing processes is particularly helpful for identifying parts of a process to improve. Process improvement includes quality assurance (QA) with clearly defined criteria that determines when an item passes QA. This feature helps to identify process defects that could have otherwise gone unnoticed.
Step 2: Identify problems and eliminate waste
Team members will often have many ideas about how to improve existing processes. It can be tempting to spend a lot of time thinking about ways to do this, but that’s not quite what continuous improvement means. Instead, team members should first define the problems they’re trying to solve, and then devise solutions to those problems.
It’s best to start with solving organizational problems, such as making better products, reducing delivery cycles, or offering more services. Lean process methodologies call these goals Objectives and Key Results (OKRs), which are used in a framework to collaboratively set and track goals.
Team members consider each of these organizational goals and how well the current process achieves them. If they can identify more effective ways of doing so, they have defined a goal for that process.
Defining team and personal goals is also part of this step, which could include reducing the time spent in meetings. The team should then develop a list of goals and a system for selecting the goals it would like to focus on. After that, the team can establish ways to achieve those goals, like only requiring essential staff members to attend meetings.
Step 3: Establish standardized work procedures
Lean process improvement requires standardized work procedures, meaning the steps for a task and their sequence are well documented. Standardizing work also includes describing who does it, how it’s done, and when they do it.
This documentation should be a collaborative process involving those who actually do the work, in addition to other stakeholders like their supervisors. Once the documentation is complete, employees can be taught the standardized work. With this documentation handy, new employees can also be onboarded and taught process procedures quickly.
Step 4: Implement continuous improvement practices
Long-term process improvement requires regular review to ensure the changes remain relevant. Even if your organization doesn’t formally practice lean continuous improvement, you can still apply changes in a consistent, sustainable manner.
However, these practices will tend to take a back seat to more urgent matters, making it critical to keep continuous improvement top-of-mind and dedicate time to it when possible.
Some teams review process improvement at every standup meeting, while others only do so at monthly or quarterly meetings. The important requirement here is to establish a regular schedule and method for discussing these initiatives.
For example, a Kanban board is an effective method for visualizing process improvement activities because they are displayed alongside other ongoing work. Leaders can also emphasize the importance of continuous improvement by encouraging team members to schedule time for it.
Step 5: Sustain improvements
The previous steps provide metrics that track the performance of process changes, but you must also act on those metrics if they are to make sustainable improvements. This requires you to determine the criteria for success before implementing any changes. You should also discuss the performance of process improvements at regularly scheduled meetings.
How do I incorporate lean process improvement into my business?
The first step in incorporating lean process improvement into an existing business is to review the process you want to improve. This step involves talking to the employees who actually perform the process, which many companies neglect.
Next, you need to identify the improvements to make, often by asking those same employees. Implementing the changes they suggest should include creating a plan that everyone understands and buys into.
Assessing the impact these changes have on operational efficiency is the next step, which usually involves multiple rounds of testing. This requires constant monitoring, so you can address new issues as they appear.
Identifying the activities that add value to the process is also essential, as it allows you to remove unnecessary activities and re-test the process. Limiting the risk of these changes involves eliminating or simplifying tasks, often by automating activities or changing the way they’re executed.
Standardizing the process requires documenting it thoroughly as you refine the changes. This practice makes the process repeatable, both by team members and other employees.
Processes also need to comply with requirements from governing bodies, industry standards and the company’s own policies. Improving customer experiences is also a crucial step in implementing lean process improvement, since any changes must positively impact customers.
Lean process improvement tools and techniques
Many tools and techniques are available for implementing lean process improvement, including the following:
Six Sigma
The goal of the Six Sigma methodology is to increase customer satisfaction by standardizing workflow. It consists of the following components:
- Define
- Measure
- Analyze
- Improve
- Control
PDCA Cycle
The Plan Do Check Act (PDCA) Cycle performs continuous improvement by repeatedly analyzing a problem, testing a solution, reviewing the changes and analyzing their effects.
Kaizen
Kaizen is a commitment towards continuous improvement, rather than a specific tool. This term is Japanese for improvement and is based on the idea that incremental changes improve processes over time.
A Kaizen blitz is a common Kaizen technique, which consists of a short sprint lasting only a few days. However, it must still be part of a continuous effort toward improvement to be considered Kaizen.
5S Method
The 5S method is designed to maintain order in the workplace and is easy to add to an existing process improvement plan. It consists of the following practices:
- Sort
- Set order
- Shine
- Standardize
- Sustain
This method was originally developed for manufacturing, however, the method can be applied to process improvement. For example:
- Sort can mean reviewing processes.
- Set order can mean organizing workflows or tasks.
- Shine can be the actual application or implementation of improvements.
- Standardize, as the name suggests, can mean documenting the improvements or plans so that they can be communicated to teams.
- Sustain can be applied to continuous improvement.
Manage process improvements with Pipefy
Lean process improvement is an ongoing process that makes organizations more efficient over the long term. It involves targeting the biggest source of inefficiency first and fixing it, before moving on to the next problem. Tackling these issues one at a time is the key to creating a well-functioning business.
Pipefy’s business process management platform offers a range of solutions for optimizing business processes. This dedicated platform reduces process clutter or bottlenecks by automating many of the manual redundancies that can occur, such as assignments, handoffs, notifications, or status updates. Its no-code user interface means that anyone can design and implement process improvements.