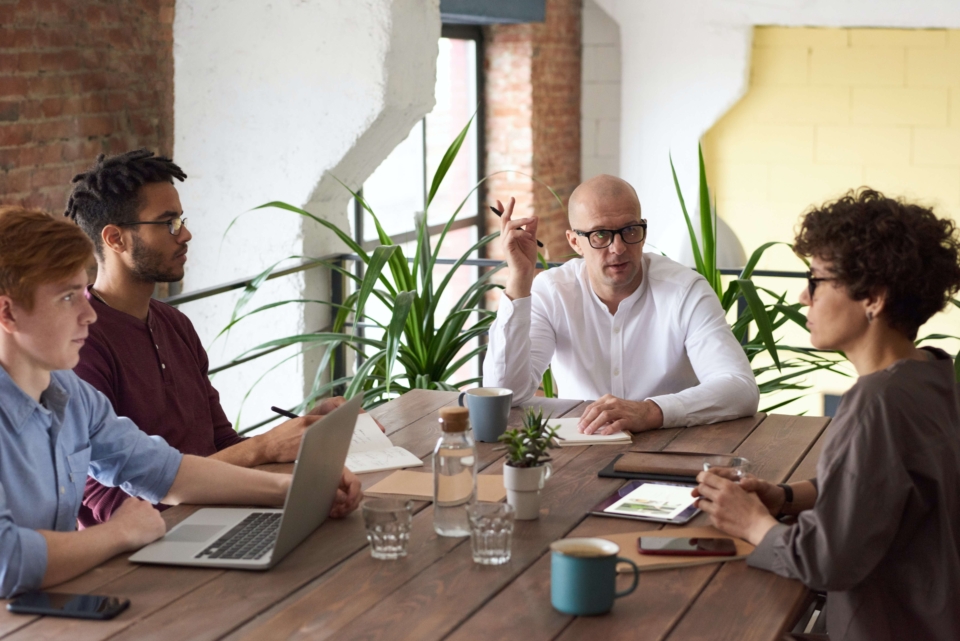
Operational planning is the creation of a detailed roadmap based on a strategic plan. It aligns action items with timelines and key milestones that an organization needs to execute the strategic plan. As a result, an operational plan outlines the organization’s key objectives and the approach it will use to achieve them.
Optimize and manage any type of workflow and business process with Workflow Management: The Crash Course
The operational planning process describes a company’s responsibilities based on a timeline that matches its typical organizational speed. This timeline is usually very dynamic, so it’s important for the plan to maintain clarity during these changes.
A sound operational plan also ensures team members collaborate with each other by ensuring everyone knows their duties as well as those of the other team members. In addition, it must guide critical decisions regarding the organization’s long-term strategy.
Operational planning definition
Operational planning is the execution of a strategic plan, making it a forward-looking process. It maps out factors like budgets, operational capabilities, and department goals to create a series of team-based activities that support the strategic plan.
Operational plans are most effective when the organization is able to obtain buy-in from everyone affected by them, which greatly increases the chances of stakeholders collaborating and reporting issues.
These actions are crucial to ensuring that the operational plan meets its milestones and deliveries. Communication across departments like business and finance is particularly important for helping an organization meet the goals of its operational plan.
Assume that a manufacturer wants to increase revenue. This plan would likely include the collaboration between departments like finance, sales, marketing, and operations to align the company’s strategies to support revenue growth.
Another example would be a brand that wants to introduce a new product. In this case, the operational plan would be to expand the manufacturer’s existing capabilities, adopt new tools and create a roadmap for the new product.
Additional examples include mapping production output to meet a strategic goal or obtaining greater clarity regarding such a goal. Operational plans may also create a more specific strategy for leveraging a particular partnership.
Learn more: What Is Operational Excellence? A Complete Primer 2023
Operational planning vs. strategic planning
Operational and strategic planning are distinct activities, although they do complement each other. Strategic plans define an organization’s business strategy and other long-term goals, while operational plans define the steps needed to achieve those goals.
An operational plan may be known by other terms, such as an operation plan or work plan. It’s a detailed outline of:
- The tasks team members will need to focus on the short term, usually within the next year, and;
- Answers to questions about these goals, including its purpose, the tasks it will involve, and who will complete them.
In comparison, a strategic plan describes:
- High-level goals,
- Long-term visions,
- The company’s overall mission, usually for the next three to five years, and
- Major initiatives that the organization must implement to meet those goals and measure its progress.
A strategic plan provides a big picture of the company’s goals, but doesn’t describe how to achieve them.
9 elements of effective operational planning
An operational plan should accurately describe the organization’s business operations, so team members understand how it works and how they can help achieve its strategic objectives.
The following list describes some of the key elements for effective operational planning.
1. Executive summary
An executive summary is usually the first part of an operational plan. This brief document summarizes the operational plan as well as other documents like business and strategic plans. An executive summary’s primary purpose is to provide busy readers with a short overview of the operational plan.
2. Budget
An operational budget estimates the costs of the operational plan for a particular time period. It also defines the amount of money available for the project, like any other budget.
Components of the budget may include equipment and raw materials, as well as any other resources needed to implement the plan. Spending must remain below the operational budget to avoid running out of resources before completing the operational plan.
3. Objectives
The objectives of an operational plan must align with the organization’s strategic objectives. For example, a strategic objective to increase sales by 30% over the next five years could result in an operational objective to hire more sales employees.
Note that an organization must develop its strategic plan first, before developing action items for the operational plan.
4. Processes and workflows
An operational plan should explain the processes and workflows that the team will need to execute to meet its objectives. This section should include required resources, such as equipment, raw materials, and staffing.
Learn more: What Is Process Management? Importance, Examples, and Lifecycle
5. Timeline
The operational plan’s timeline will usually be shorter than the strategic plan. In some cases, an organization may develop a series of operational plans to cover its entire strategic plan. While the timeline for a typical operational plan is usually less than a year, the length is primarily based on the duration of the necessary processes and workflows.
6. Hiring plan
Operational plans often identify skills gaps in the existing team, requiring the project manager to hire additional members. In some cases, it may be necessary to create an entire department to implement all of the workflows in the operational plan.
7. Quality assurance and control
Quality assurance and control procedures are usually a key component of operational plans, especially when it involves regulatory compliance or customer safety. In addition, these issues can cost a company millions of dollars if they aren’t handled correctly.
8. Key performance indicators (KPIs)
An operational plan must define the KPIs it will use to measure the performance of its business operations. The set of KPIs described in the operational plan can be extensive, as they often need to cover many areas of operations, such as product development, marketing, and sales. KPIs commonly used in an operational plan include the following:
- Number of 5-star reviews received
- Number of customers acquired
- Number of customer service cases closed
- Product launch deadlines
- Number of manufactured goods
- Revenue increased by a certain percentage
- Number of working hours saved
9. Constraints and risks
Additional components of an operational plan include its risks, such as security vulnerabilities that could be created during implementation. Time and resource constraints are also required components of an operational plan, especially if they could impact business operations.
Learn more: Operational Efficiency: Definition, Examples, and Strategies
Operational planning process: step-by-step guide
The major steps of operational planning include the following:
- Assessing the situation
- Setting goals
- Developing action plans
- Allocating resources
- Monitoring progress
- Revising the plan
Step 1: Assess the situation
Assessing the organization’s current strategy is usually the first step in developing an operational plan. This step generally includes an analysis of the plan’s tasks and activities, especially the ones that are key to achieving its goals.
An operational plan typically provides the project manager with the flexibility to break high-level tasks into smaller ones that are easier to assign. Assessing strategic goals also helps ensure that the goals of the operational plan align with those of the strategic plan.
Step 2: Set goals
You must clearly define the goals of an operational plan before setting it into motion. A good approach to meeting this requirement is to assess the current team’s priorities and productivity, and compare it to the company’s vision.
A project manager can then develop the operation plan’s objectives, usually after discussion with the team. These goals should also be prioritized at this time to ensure the best allocation of resources.
Step 3: Develop action plans
Action plans, also known as business plans, guide the operational plan’s daily activities, including what needs to be done, when it needs to be done and what resources it requires. They convert strategic objectives into actions the planning team can perform, such as funding a proposal, applying for a loan or obtaining stakeholder buy-in for the operation plan itself.
Action plans vary greatly in details, but they generally contain many of the same elements. For example, they usually begin with a statement of the action plan’s purpose, such as output or result area. Action plans should also describe the steps needed to achieve this objective.
An action plan should include a schedule for each step, with dates for its beginning and end. In addition, they should assign one or more team members who will be responsible for completing each step. In many cases, an action plan will provide greater clarification on resource requirements than the operational plan itself.
Each step in the action plan will also address these components in greater detail. The end result of this planning process should provide a practical approach for resourcing and implementing each step towards the operational plan’s ultimate objective.
Step 4: Allocate resources
The manager or person in charge of executing on the business strategy or strategies must plan the operational plan’s budget, according to the projects and tasks that the team plans to complete.
Considering the budget while developing tasks also helps managers identify the tasks that are feasible under the existing financial constraints. In addition, managers should take the team’s current commitments into account when estimating the resources that the operational plan will require.
They also consider the competency of their team members in most cases, including existing skill sets and experience. Finally, most managers solicit opinions from their team members when allocating resources for an operational plan.
Step 5: Monitor progress
Project managers must document each step of the operational plan as it proceeds. This practice allows them to track progress and measure improvement over time. It also provides managers with useful insight they can apply when developing the next operational plan.
Documenting the plan’s progress also helps team members remain updated on project developments, especially those of other departments. Company executives also monitor progress to obtain a high-level view of the project, especially task completion times.
Step 6: Revise the plan
Project managers must remain flexible when developing an operational plan, as it will change frequently after implementation begins. This trait allows them to accommodate the challenges that will inevitably arise while executing the plan. In particular, managers need to change the priority of tasks or reassign them based on poor performance.
Assume, for example, that the activities initially specified by the operational plan fail to meet their stated goals. It might be necessary to revise those plans if those goals are now unrealistic. Managers typically meet with their team members on a regular basis to review possible changes to an operational plan.
Best practices for operational planning
Managers should adopt multiple practices to provide their operational plan with the best chance of success. These best practices include:
- Using the strategic plan to shape the actions of the operational plan.
- Knowing the budget before they even start developing an operational plan, including how the current budget compares with those of previous years.
- Having a clear overall picture of the project’s current status, including the team members and other resources available.
- Ensuring that the goals of the operational plan are achievable in practice.
Other best practices for developing an operational plan include selecting the methodology and tools that the team will use. Finally, managers must choose the KPIs that will best measure the operational plan’s project, as well as the benchmarks for each KPI.
Common challenges that limit effective planning
Human errors
Operational planning involves many challenges, although they’re typically the result of human error or interdependencies between parts.
Human error is a routine problem in manufacturing processes, especially when transitioning a product from production to sale.
Also read: How to Automate a Manual Process
Poor cross-functional collaboration
Operational planning teams should be cross-functional, so they can effectively communicate with diverse departments like accounting, engineering and human resources. This feature allows the team to obtain a clear understanding of each department’s end goals.
Lack of task coordination
Interdependence of parts is one of the primary disadvantages of implementing an operational plan. Success depends on coordinating the plan’s many tasks, many of which are in progress at the same time.
As a result, the failure of one task often adversely affects other tasks, especially those that are subsequent to the one that initially failed. This characteristic creates the potential for the entire operational plan becoming useless unless the manager revises the plan quickly and correctly.
Unlock business efficiency with Pipefy for operational planning
Boost your company’s performance by ensuring each project is properly planned. With Pipefy’s no-code business process management platform lets teams monitor and manage the progress of processes easily. With real-time process dashboards, Pipefy collects and shares data quickly so teams can milestones and bottlenecks to stay on track.