ARTICLE SUMMARY
Have you ever found yourself with one of those tricky problems that seemed to be unsolvable? Well, it happens to the best of us, but here, I’ll show you a workaround with A3 Methodology — the Lean problem-solving tool. Spoiler alert: it was built to help Lean teams solve problems in their manufacturing plants, but the magic is that A3 can be used in any company (whether they are focused on delivering products or services) and by anyone (even by professionals who are not familiar with Lean thinking yet.)
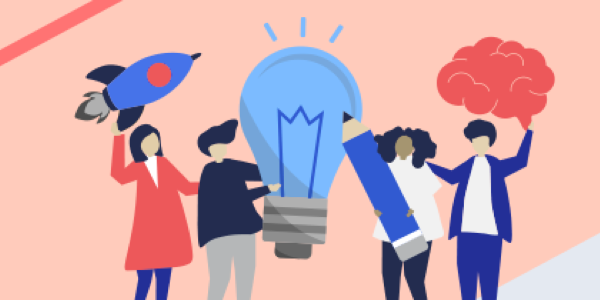
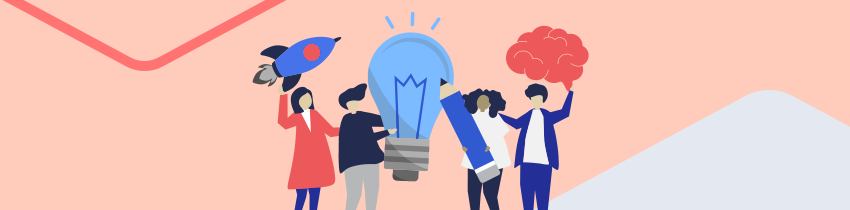
Have you ever found yourself with one of those tricky problems that seemed to be unsolvable? That no matter how much you dug, you still struggled to identify the root causes of that problem? Well, it happens to the best of us, but here, I’ll show you a workaround with A3 Methodology — the Lean problem-solving tool. Come with me:
What is an A3?
Born in the manufacturing environment, the A3 Methodology is one of the main tools of the Lean management philosophy. It was built to help Lean teams solve problems in their manufacturing plants, but the magic here is that A3 can be used in any company (whether they are focused on delivering products or services) and by anyone (even by professionals who are not familiar with Lean thinking yet.)
First of all, it’s important to understand that collaboration and continuous improvement are intrinsic parts of Lean thinking, therefore, they are intrinsic parts of the A3 Methodology. In other words, using this tool won’t be effective if it’s a top-down practice. You must involve everyone in the team. As you can see in our Beginner’s Guide for Future Lean Experts, “the idea is to involve people from every hierarchical level in the problem-solving process.”
So if you want to solve problems, plan the future state of your processes and operations and report the status of a situation, you can and should explore the A3 Methodology with your team.
The tool consists of discussing seven basic aspects:
- Background: what are you talking about and why?
- Current Conditions: what is the situation now?
- Targets/Goals: what is the expected outcome of this process?
- Analysis: why is there a problem and why is this process necessary?
- Proposed Countermeasures: what does the group think should be done and why?
- Implementation Plan: how will you implement this effectively?
- Follow Up: how will you ensure that all of the talk will become action?
But before starting to answer these questions, it’s important to understand how you can effectively build an A3:
Types of A3
When researching for A3, you’ll probably find different models. Some with charts and tables, some with drawings and some even in a more conceptual shape. The thing is: there isn’t a definitive format for it as long as you manage to answer all the seven questions above in a clear and effective way.
If your process demands a more visual and colorful solution, go for it. But if you need something more direct and descriptive, also feel free to do so. It’s important here to keep in mind that every process is unique and can be better explored in different configurations. Remember you can perform this digitally, printed and even hand-drawn.
Easy Steps to Build an A3 for Problem-Solving
Now it’s time to get hands-on. Let’s do this!
- Remember what I told you about collectivity? Well, now it’s time to get everyone ready. The first step here is to mobilize your team. When talking to people, don’t forget to explain why they are being chosen for the job and how important it is to improve your processes and performance. Pro tip: When picking your squad, don’t forget to involve people from the entire process chain. Leaders, analysts, interns and even temporary employees—here you want to work with whoever gets the work done.
- After gathering everyone together, it’s time to grab an A3 paper size (yes, that big 29,7 x 42,0 cm piece of paper!) and start writing down the seven questions in different squares. Don’t be shy: use the entire page when drawing the squares. Pro tip: Here it’s nice to insert the date, title of the document and the team in charge. If you want to check it later and/or share it with other departments, these pieces of information are important to keep your A3 and files in order.
- Now let’s answer those questions. Now’s the time to reflect on what options of content you’ll use to fill in each box. Will you need charts and tables? Are you going to draw something? Do you want to insert other Lean tools inside your A3? Which metrics are you going to use? Here, the sky is the limit as long as it helps you answer the questions accurately. Pro tip: Even though you don’t need to know Lean to use A3, it’s nice to broaden your knowledge and perspective. Here’s our Beginner’s Guide for Future Lean Experts and the Lean Hub. You’ll discover everything you need to know about Lean management there.
- You and your team did it—great job! Now it’s time for all of you to analyze your A3 and brainstorm how you’ll cut your problems at the root. How are your results according to your metrics? Did you manage to find the root cause of your issues? How can you solve your problems optimizing resources? Explore all the data you manage to extract from your A3.
See, it’s not hard. It’s actually a fun way of connecting with your team and improving everyone’s performance together. You just have to always keep in mind that:
- Lean and A3 are people-driven
- A3 should never be a top-down initiative
- It’s more valuable to solve problems together with your team
- The sky is the limit when designing your A3 – use whatever piece of information is relevant to you
- Enjoy this time to better know your people
- Have fun!