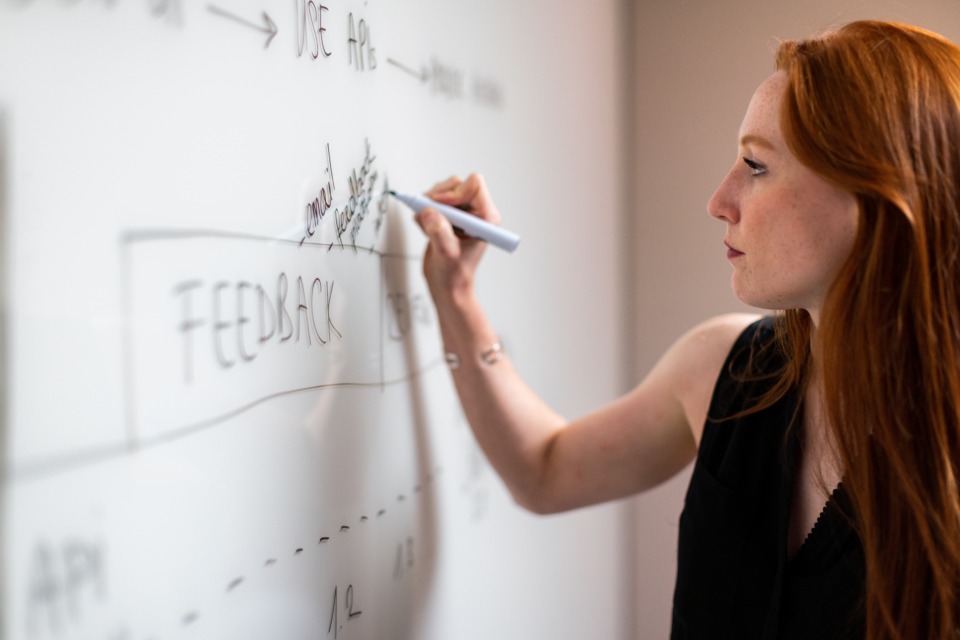
One of the best ways to scale your business is by identifying bottlenecks and inefficiencies to streamline work processes. In today’s rapidly changing business environment, it’s more important than ever to implement process improvement methodologies that allow you to make changes and meet customer demands, and that saves both time and money in the long run.
There is no one-size-fits-all approach to improving business processes and maximizing efficiency. Every business is different and the methodology that works best for yours might not be the most efficient for another, which is why it’s important to test multiple methods and only then choose the one that produces optimal results.
In this guide to process improvement, we’re going to discuss some of the most common process improvement methodologies, how to decide which methodology to use, and how to identify process improvement needs.
Build better workflows with the Definitive Guide to Workflow Management
What is a process improvement methodology?
A process improvement methodology is a systematic approach to evaluating current processes and then adapting them. The goals of any process improvement methodology are to improve productivity, adapt to new business needs, and streamline workflows, in order to ultimately reduce costs and increase revenue.
Rather than simply taking a shot in the dark with your business processes, these methodologies allow companies to define improvement opportunities, implement changes, and then test these changes against previous process performance. It is an analytical approach that uses hard numbers and data to compare the before and after, clearly showing what worked and what didn’t.
These methodologies make it easy to track those changes and then make way for another optimization attempt. By following a process improvement methodology, your business will be well on its way to streamlining your most essential workflows and business processes, saving time and money, achieving operational excellence, and increasing employee productivity in a significant way.
What are the most common process improvement strategies?
When it comes to implementing process improvement methodologies, using the strategies most commonly utilized by other businesses and enterprises in your industry is a great way to get started with what’s been proven to work.
Some of the most common process improvement strategies used today include six sigma, the PDCA cycle, Kaizen, continuous improvement, TQM, the theory of constraints, 5S, SIPOC analysis, process mapping, value stream mapping, Kanban, and business process automation.
Each improvement strategy has its own pros and cons, which is why it’s crucial to pick a strategy whose strengths match that of your particular industry or niche.
Keep reading or skip to the section on the 12 types of process improvement methodologies for a deeper understanding of each of these process improvement strategies, how they work, and what they can do to optimize your company’s processes and workflows.
How to identify process improvement needs
Before you implement a process improvement methodology or strategy, you must first identify the process improvement needs that are currently present within your organization.
Some of the best ways to identify process improvement needs include:
- Listening to feedback from employees
- Listening to customer feedback
- Looking for recurring issues or problems that have been documented more than once
- Tracking metrics and data and looking for anomalies or inefficiencies
- Getting ideas for process improvements from competitors
- Identifying proven improvements from new scientific research or studies
The common theme that stems from all these process improvement identification methods is that they all involve talking to the individuals working with those processes frequently, looking at data, and getting ideas from improvements others in your industry are implementing.
In addition to identifying process improvement needs, you also have to identify the inefficiencies within processes. When you and your team keep a close eye on how your processes currently operate, you’ll start to see plenty of improvement opportunities that you can act on.
12 types of process improvement methodologies
There’s no single process improvement methodology that stands above the rest. No matter which improvement method you choose to pursue in your own organization, there are pros, cons, strengths, and weaknesses to each.
Whether you’re interested in implementing process improvements to improve employee productivity, cut down on manufacturing costs, or improve process efficiency, learn more about these popular process improvement methodologies to get started.
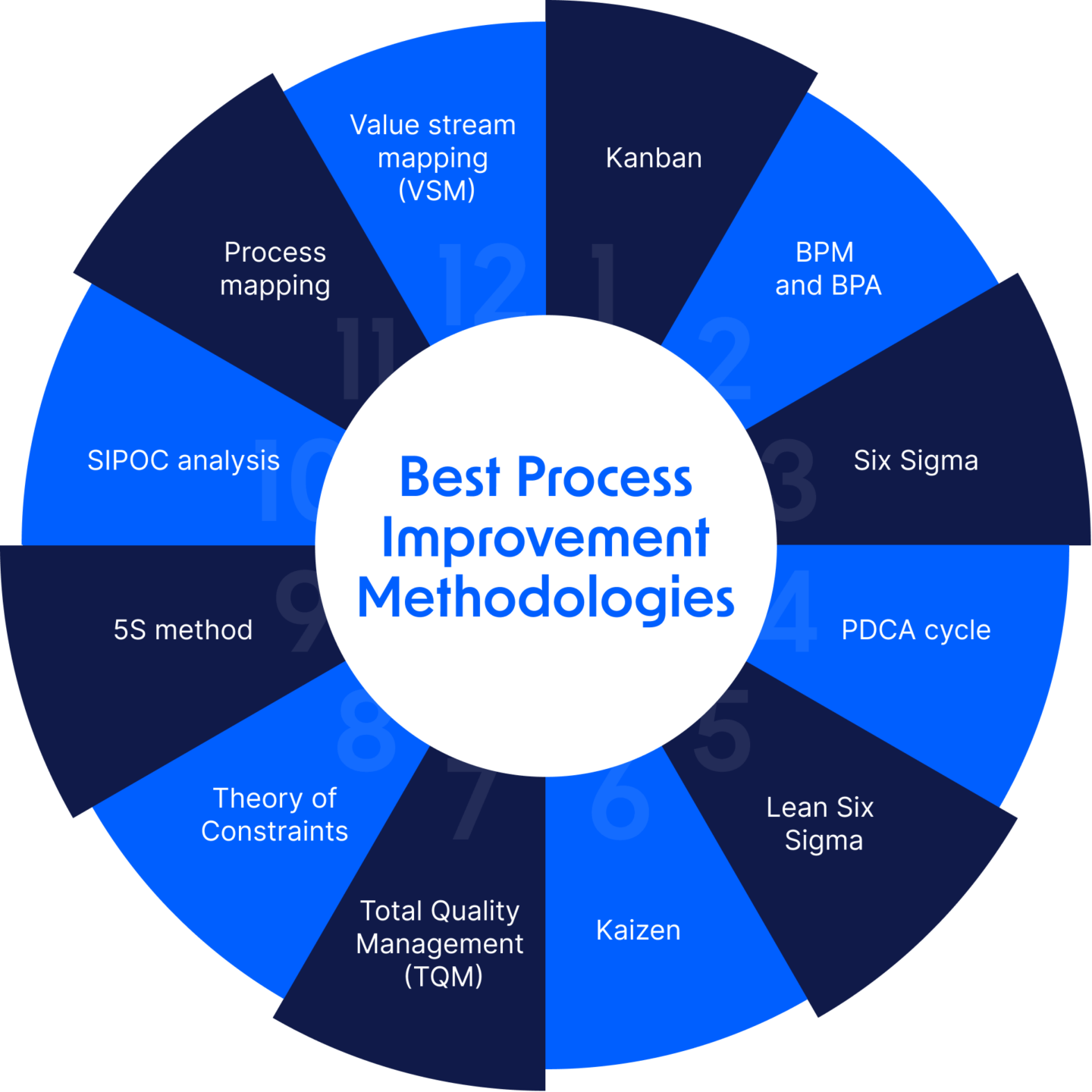
1. Six Sigma
Six Sigma is a process improvement strategy that was first introduced at Motorola for quality improvement, later making its way into General Electric and many other manufacturing companies and businesses.
The primary goal of this process improvement strategy is to help companies measure inconsistencies and defects within a process to deliver the best products and services they can muster to their loyal customers.
This is done through the five stages of process improvement: define, measure, analyze, improve, and control, or DMAIC.
Since Six Sigma relies on statistics and data in order to make decisions more so than the other methodologies we’ll describe, the define, measure, and analyze steps are most important for determining the improvements required and articulating these improvements in terms of specific data.
After the required improvements have been defined, the improvement and control steps address the root causes of the problems found and then control the improved process to correct any defects or deviations.
2. PDCA Cycle (plan, do, act, check)
The PDCA cycle methodology was originally created by Walter Shewhart who applied the scientific method to his work in economic quality control. It was built for interactive problem-solving and process improvement. In time, this method was advanced further by W. Edwards Deming, who also applied it to process improvement and quality control.
The four primary steps to the PDCA cycle include planning, doing, checking, and acting. In the planning process, your business decides on the problem you need to solve and develops a solution. You then move into the doing stage, where you test the plan and implement it on a small scale.
After the first two steps are complete, you’ll move into the checking and acting stages which involve checking the results of your doing stage and deciding whether or not you’d like to roll out this change on a larger scale.
The essence of PDCA is to test improvements to business processes on a small and controlled scale, and, if they work, then roll them out to the rest of your processes and workflows.
3. Lean Six Sigma
Lean Six Sigma combines the PDCA methodology and the Six Sigma methodology all in one. This methodology can be used to improve business processes by utilizing tools, such as the 5S method, and removing waste using the PDCA and the DMAIC method and control charts from Six Sigma.
This results in a strategy that has superior problem-solving capabilities and a proven way of implementing, testing, and controlling improvements in order to verify that they work as intended.
4. Kaizen (continuous improvement)
The Kaizen, or continuous improvement methodology, centers around incremental, regular improvements to various workflows and manufacturing processes. The core idea of Kaizen is that by utilizing the strengths of collective teams within an organization, a powerful improvement engine can be created.
The strength of Kaizen is that it utilizes employees at all levels of an organization and places them into the improvement process, everyone from leaders and managers to employees.
Kaizen works by setting goals, providing background information, reviewing the current state of business processes, and identifying required improvements.
Next, those improvements are implemented and reviewed for what worked and what didn’t. The results are reported, and a new cycle can be started for additional improvements as required.
5. Total Quality Management (TQM)
TQM, or total quality management, is a continuous improvement process that aims to do the right things from the very beginning and every time, with the consumer being the ultimate judge of quality. This differs from methods like Kaizen, where the employees were primarily responsible for judging quality.
In TQM, the focus is on customer satisfaction, commitment by employees, adherence to processes, and utilizing data to eliminate errors and bottlenecks.
Since TQM aims to do everything right from the very beginning, this method is heavily invested in education, training, leadership, communication, and having the right organizational support structures in place. This also involves developing incentives, including employee rewards and recognition, to help improve workflows and processes.
Over time, TQM has given way to a newer approach to process improvement and is more commonly referred to as business process management. (More on that later.)
6. Theory of Constraints
With the Theory of Constraints approach, bottlenecks and process improvements are seen through a scientific lens. The most important limiting factor, or constraint, is first identified. This is the ultimate item that stands in the way of achieving the organization’s goals and the improvement they seek.
Once this constraint is identified, it is systematically improved until it no longer interferes with business processes and is fully optimized.
7. 5S method
The 5S method is an improvement methodology that was originally created by the Toyota Motor Corporation to help maximize employee productivity by establishing a safe, clean, uncluttered, and well-organized workplace. The 5S method is derived from five Japanese terms: seiri (sort), seiton (set in order), seiso (shine), seiketsu (standardize), and shitsuke (sustain).
When applied to process improvement, the 5S method can be implemented by:
- Identifying a business process that needs to be improved, and sorting what is needed and not needed with the help of process owners or managers.
- Organizing or “setting in order” tasks, steps, information, and flows of approval.
- “Shining” or cleaning up the process by looking for redundancies or automating manual tasks.
- “Standardizing” and “sustaining” these improvements via continuous improvement cycles.
8. SIPOC analysis
A SIPOC analysis is a process improvement method that is an acronym for suppliers, inputs, processes, outputs, and customers. Oftentimes, a SIPOC analysis is perceived as a diagram or business process map that shows all of the inputs, outputs, connections, and decision points present in a workflow or process.
These diagrams are used to bring alignment between all of the stakeholders of a process, making it more efficient and fixing any issues or bottlenecks.
9. Process mapping
Process mapping is similar to a SIPOC analysis in that it is a detailed diagram showing business processes in a visual format. When a process is mapped out, it allows everyone involved in that process to see it clearly in a visual format and, therefore, make improvements and markups as required.
Learn more about process mapping techniques and flowchart symbols.
10. Value stream mapping (VSM)
Value stream mapping, or VSM, is a process improvement strategy that involves mapping out the series of steps required to produce and provide the product or service customers need. In a value stream map, a visual representation of the key steps and data required to complete the delivery process is compiled and can then be understood by all stakeholders in order to make improvements.
11. Kanban
Kanban is a Lean workflow management tool that’s used to manage, define, and improve product and service delivery for organizations. Kanban is the Japanese word for “visual board” which is exactly what this tool is — a visual board with “cards” that are moved from left to right as a process is completed.
Oftentimes, the columns of a Kanban board include requested items, items that are in progress, and items that are completed. As your organization works through processes, you can easily move tasks and to-do items from one segment to another to visually see progress.
12. Business process management and business process automation
Business process management (BPM) and business process automation (BPA) are a structured approach to improving the workflows and processes within your organization, as well as taking the steps required to automate repetitive tasks to save time, save money, and improve productivity.
With BPM and BPA, various methods are used to model, analyze, measure, optimize, improve, and automate your business process. Depending on the complexity of your processes, the exact steps you use to take your workflows from their current state to an automated process can vary.
Today, many companies rely on low-code automation as part of their BPM strategy.
What is the best methodology to apply to my business process?
Every single one of the business improvement methodologies discussed has its own strengths and weaknesses, so there isn’t a right answer to these questions.
However, if your business is involved in manufacturing or is seeking a data-driven approach to making process improvements, consider Six Sigma, PDCA, or Lean Six Sigma can be a great place to start. If the goal is to have visibility into the status of all process improvements being implemented, consider Kanban.
Or, if you need insight into key steps of a process to understand how to provide the best product and customer experience, consider a process improvement strategy like value stream mapping.
The key to finding the right method for your organization is to test multiple methods and see which ones your team resonates with, enjoys using the most, and leads to the best results.
Structure and manage process improvements easily with Pipefy
Pipefy is a process improvement and automation tool that makes it easy for teams to build and manage any type of business process. Pipefy integrates with the components of the existing stack to close gaps, dissolve silos, and help teams create structured processes that deliver consistency and efficiency.