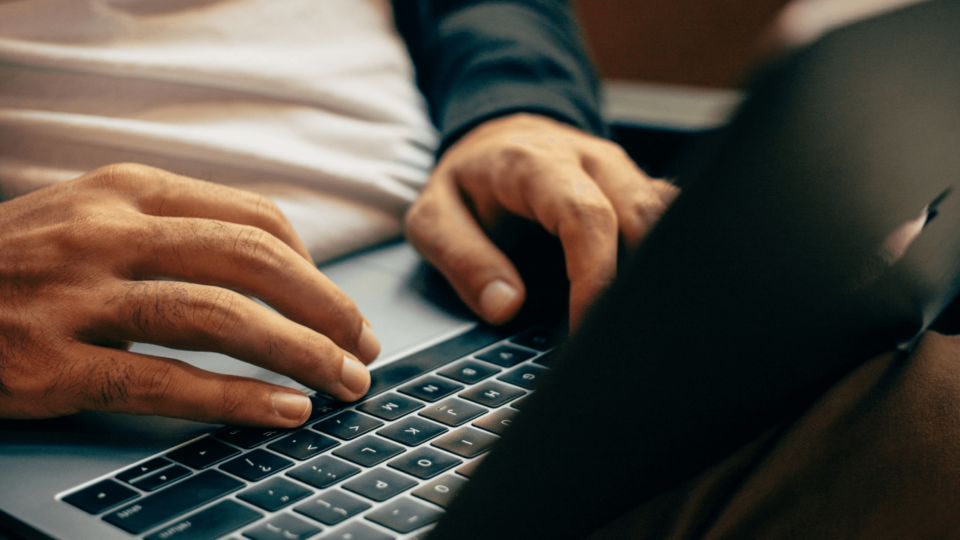
Process improvement tools are the gateway to operational efficiency. That’s because over time, processes need to be continually optimized so that they remain effective and efficient as the business evolves. Today, we will give you Top 10 Process Improvement Tools to transform business operations.
Build better processes with the Definitive Guide to Business Process Automation
What are process improvement tools?
Process improvement tools are specific techniques used to evaluate processes and identify opportunities for their improvement. These tools are typically thought of as methodologies, but in many cases, software is also involved.
All process improvement tools — regardless of type — typically include the following activities:
Process mapping | Identifying all the elements of the current process. |
Process analysis | Reviewing the current process in detail with an eye toward optimization |
Process optimization | Implementing automation, integrations, and other changes to create a new version of the process that aligns with business goals and current resources |
Why rely on process improvement tools in businesses?
The reason why businesses rely on defined tools to improve their processes is that these tools have a proven track record for delivering results. Process improvement tools are structured methodologies that help organizations uncover improvement opportunities and systematically apply the optimizations they need to reach their goals and achieve operational excellence.
Process improvement starts with an objective assessment of the current process. These tools are designed to help business leaders and process managers understand how their current processes work, identify problems, and apply solutions.
What are common KPIs for process improvement?
Key performance indicators (KPIs) are metrics that we can use to measure the effectiveness and efficiency of any process, in relation to a business goal. The higher the performance, the better the process is at helping the business achieve its goals. These KPIs are sometimes referred to as process performance metrics.
KPIs vary from process to process. What makes sense as a measurement for an HR process may not be a meaningful measurement of a process in the finance department or for the sales team. Regardless of the type of process, the KPIs need to be quantifiable and measurable.
Examples of KPIs by process
General KPIs | Cycle time Productivity (output/input) Process cycle efficiency (value-added time/cycle time) CapacityQuality |
Request management | First response time% closed within target lead time Average handling time (AHT) Time to closeBacklog |
Human Resources | Average recruitment time Cost per hireEmployee productivity Employee satisfaction |
Finance | Accounts payable process cost Budget creation cycle time Payment error rateInternal audit cycle time |
Customer Service | Total tickets Tickets per customer First response time Average handling time (AHT) Time to resolution (TTR) Cost per resolution (CPR) Volume by channel |
IT | Total tickets First response time Average handling time (AHT) Time to resolution (TTR) CapacityBacklog |
Sales | First response time Monthly calls or emails per rep Sales per rep Sales by contact method Customer acquisition cost |
Top 10 Process improvement tools
1. Business process automation (BPA)
Business process automation is software that helps teams improve the efficiency of their processes by reducing manual effort, avoiding errors, and orchestrating their processes into a unified whole. BPA provides a visual interface that allows non-technical users to build, modify, and automate their processes easily, without having to submit a ticket each time a change is needed.
BPA tools are the best choice for businesses looking to automate and optimize processes in any department. BPA is adaptable, integrates with current tech stack components, and delivers many features and capabilities that lead to better processes. These include low-code automation, guest portals and forms, dashboards, and process orchestration.
Learn more about business process automation.
2. Business process management (BPM)
BPM is sometimes thought of as software, but it’s really the discipline of identifying, evaluating, and optimizing individual processes in order to achieve business goals. BPM uses a variety of techniques and tools to improve business processes.
BPM approaches process improvement from a business strategy perspective, in order to align each process with the overall business goals. Common BPM tactics include process mapping, process modeling, analysis, and continuous improvement. BPM relies on a structured framework in which processes are identified, measured, analyzed, and then improved.
Because BPM is complex, many companies use BPM software to improve their processes. Increasingly, BPA tools are being used to achieve BPM goals.
Learn more about business process management.
3. Business Process Reengineering (BPR)
Business process reengineering (BPR) is a model of process change in which processes are evaluated and then redesigned and reorganized. The goal of BPR is to significantly improve the process metrics such as efficiency, quality, and speed. Unlike other process improvement tools in which changes are made incrementally, BPR often completely overhauls processes. While these types of sudden changes are sometimes necessary, they can also be seen as disruptive.
James Champy and Michael Hammer developed the BPR model in the early 1990s in their book Reengineering the Corporation: A Manifesto for Business Revolution. BPR was widely embraced by businesses after its introduction. Today, much of its framework takes place within the broader strategy of business process management (BPM), which is considered to be an updated version of BPR.
4. Six Sigma
Six Sigma is a methodology that takes a mathematical approach to process improvement. First developed by an engineer at Motorola in the late 80s, Six Sigma aims to reduce variance and defects in the manufacturing process. The name “Six Sigma” refers to statistical modeling and the number of deviations that occur in a specific amount of output.
Six Sigma is a highly structured method of process improvement that initially was used for manufacturing processes, but has since been applied to other types of processes. Six Sigma starts by defining a specific goal such as “improve response times” or “reduce the number of errors.”
Once the goal is defined, Six Sigma uses a five-phase methodology to identify and achieve the necessary process improvements. These five phases are define, measure, analyze, improve, and control, often referred to as DMAIC.
5. PDCA cycle
Another tool businesses use to improve their processes is what is known as the PDCA method. PDCA is the acronym for plan, do, check, and act. This model of process improvement is based on the scientific method: hypothesize, experiment, evaluate. PDCA is an iterative approach, which means that PDCA will be repeated until the desired results are achieved.
6. Gap analysis
Gap analysis is a rather straightforward approach to process improvement that involves an assessment of the current process, developing a model of the ideal process, and then determining what is required to move from the current state to the desired state.
Gap analysis may involve the use of SMART (specific, measurable, achievable, relevant, and time-sensitive), and the development of a process improvement plan.
7. Root Cause Analysis (RCA)
The idea behind root cause analysis is that any time there is a problem with a process, it is possible to identify a single action or condition that leads to the problem. By identifying this root cause, process managers can resolve the problem at a higher level. In some ways, RCA is similar to gap analysis.
This type of analysis commonly looks for the following types of root causes:
- Events
- Changes
- Barriers
- Oversights
In addition, a root cause analysis might involve the analysis of situations, problems, solutions, and potential problems. Diagrams are often used in root cause analysis.
8. Statistical Process Control (SPC)
Statistical process control (SPC) is a process improvement tool used primarily in manufacturing. SPC relies on statistical analysis and other methods to control the quality of production processes. More specifically, SPC looks to distinguish normal or common variations from special variations. When a process features special (abnormal) variation, it is considered to be “no in control.”
9. Total Quality Management (TQM)
TQM, or total quality management, is a comprehensive approach to improving all processes within a business.TQM was developed in the late 1970s.
Total quality management aims to create a culture in which employees are empowered to continuously improve the processes they use. This applies to all employees in every department, including sales, marketing, production, customer service, finance, and others.
Unlike other process improvement tools, TQM does not define a particular methodology. Instead, the methodology is determined by the department, resources, and type of problem to be solved. TQM is much more flexible and comprehensive than other process improvement strategies.
10. Process diagrams
Diagrams are one of the most effective tools for process improvement. Diagrams help us visualize and document processes in order to better understand how work gets done, how information is shared, and where bottlenecks, delays, or errors are likely to occur.
There are a few different types of diagrams that can be used to improve processes. Below are examples of the most common.
SIPOC diagram
SIPOC is one of the simplest types of workflow diagrams. SIPOC is an acronym that stands for “Supplier, Input, Process, Output, Customer.” A SIPOC diagram provides a high-level overview of your workflow or process, from left to right.
Swimlane diagram
A swimlane diagram organizes the workflow into different lanes, each of which relates to a specific person or team. This type of workflow diagram makes it easy to see who is responsible for each step of the workflow. It also provides a view into the handoffs between people or teams as work progresses through the flow.
Flowchart diagrams
Another way to illustrate your workflow is with a flowchart diagram. These visualizations rely on standard flowchart symbols to add additional information about each step in the workflow, and to make it easier for external stakeholders to understand what happens during each step.
Value Stream Mapping (VSM)
Value stream mapping is a method of process improvement that relies on a detailed inventory of all steps, activities, and tasks in a process. VSM considers each of these components, along with handoffs, information flow, and other elements of the process to identify opportunities for improvement.
VSM efforts typically begin with a value stream map. This is a type of diagram that illustrates the process in its entirety.
Learn more about value stream mapping.
Improve your processes with automation
Processes are the building blocks of business, and every company has a wide variety of them. Pipefy’s low-code AI process optimization makes it easy for teams to build, optimize, and automate any type of workflow, no coding experience required. Also, AI Agents unlimited potential is capable of eliminating repetitive and manual task, so your team can focus on what really matters.