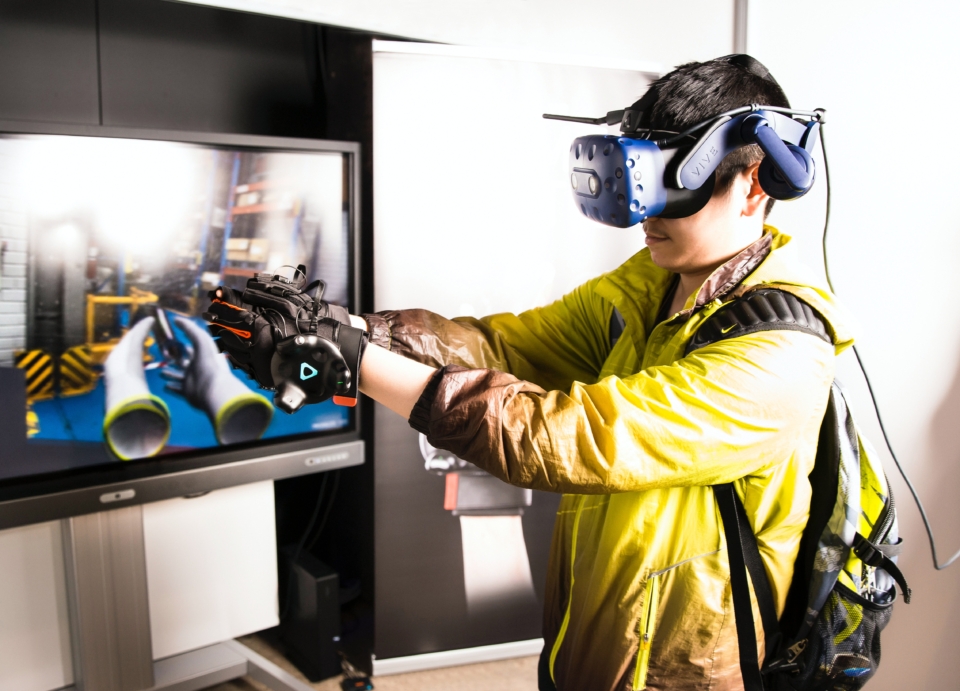
Today’s businesses must maintain a flexible approach to changing and updating their processes. Disrupting factors like market instability, new business models, and technological advances in artificial intelligence (AI) and big data are shaking up traditional operations.
Organizations must plan and analyze scenarios carefully before making sweeping decisions that affect the entire business. This sometimes requires simulating processes before implementing them so that business leaders can conduct experiments, monitor specific workflow patterns, and assess results.
This guide explores business process simulation, its benefits, and the steps for its successful implementation.
Build better workflows with the Definitive Guide to Workflow Management
What is process simulation? What is its goal?
Process simulation is a model-based approach for using software to represent technical processes, including those based in biology, chemistry, and physics.
The primary requirements for these simulations are the physical and chemical properties of the components and their reactions to one another. Mathematical modeling techniques allow the software to predict the resulting processes.
The goal of process simulation within the context of business operations is to increase process efficiency, which ultimately increases a company’s profitability and competitive advantage.
Process simulation is an effective way to optimize processes because it allows businesses to “play out” scenarios without disrupting their existing operations. It’s made possible by the creation of a process’ digital twin, which it uses to make changes. This approach allows businesses to identify and resolve potential issues before implementing a new process in the real world.
Process simulation vs. digital twinning
Process simulations and digital twins both replicate processes with digital modeling techniques, but there are distinct differences in how they do it. These include the modeling type, change type, and scope of use.
Process simulation uses Computer-aided design (CAD) models that allow the tester to introduce and test different design elements and parameters. These models are static — they don’t change until the tester introduces new elements.
A digital twin begins the same way, but in this model, data is introduced in real time. This difference means that a digital twin can be altered far more aggressively and accurately than process simulation. The digital twin can actually mature as the tester adds data and fine-tunes the process.
A simulation shows what could happen to a product under a particular set of circumstances, but a digital twin replicates the effects changes would have on a product in the real world. Testers are only limited by their imaginations in making changes to a simulation.
On the other hand, a tester can use a digital twin to determine whether or not a product is working as intended based on actual use, because it offers real feedback. A digital twin therefore has greater applications in manufacturing, which requires real data to react to changes. As a result, the changes in a simulation are purely theoretical, while the changes in a digital twin are real.
Simulations and digital twins also have a different scope of use. A simulation lets designers test different scenarios based on a CAD design and pre-defined parameters, making it most suitable for testing product designs.
A digital twin has a wider scope of use, so testers can use it for all stages of the product’s lifecycle. The applications of a digital twin are only limited by the data available for that workflow, allowing them to be used in larger decisions than simulations.
Why is process simulation important?
The overall benefit of process simulation is that it allows an organization to find ways of improving its processes, thus advancing process excellence. It also identifies the problems of existing processes and risks of changes, typically as part of process analysis. Process simulation thus allows organization leaders to make better-informed decisions.
Enhances process excellence
Simulations provide a cost-efficient, risk-free method of improving complex processes. They identify underlying factors and analyze their role in contributing to a process’s poor performance, allowing organizations to develop improvements.
The capabilities of the simulation technology are crucial to testing process changes that would be too costly or risky to test in the real world.
Simulations are also effective in engaging team members who design and develop process changes. Detailed three-dimensional (3D) models are relatively easy to make with tools that use the latest advances in graphics, and they allow teams to physically see the changes. This capability is essential for identifying the change’s potential risks and benefits. An animated 3D image can thus illustrate the value of an improvement to a process in a way that words can’t.
Identifies risks and problems
Simulations are also useful for identifying bottlenecks and other areas of improvement in a process. Modeling and analyzing process behavior with software also provides the user with a better understanding of how a business works. This information is vital for running that business more efficiently.
Tests changes
Simulations give you the means to test scenarios in a controlled environment to identify the changes that would be most beneficial to your business. Analyzing these scenarios allows you to understand what would happen to your process if you made those changes, without the risk of an actual implementation. You can improve the efficiency of your business without risking its security and data integrity.
Empowers better decision making
Simulations, which provide modeling and process behavior analysis, allow businesses to make pre-tested, on-target decisions. They also accelerate the decision-making process by testing multiple scenarios much faster than real world conditions allow. The ability to understand exactly how a proposed change will affect a process gives users foresight that enables them to identify and solve problems quickly.
What kinds of processes can be simulated?
The core functionality of process simulation is to develop models that accurately represent real processes. Model development is based on general engineering principles and specific disciplines. Processes that lend themselves to mathematical and computer modeling techniques are strong candidates for simulation.
For example, chemical and control engineering are commonly used to simulate processes in a petroleum refinery. Thermophysical properties like caloric data, vapor pressure and viscosities are often used to develop models for predicting chemical reactions in these cases.
Apparatuses like distillation columns, pumps, and reactors also have properties that companies simulate before building facilities to test functionality, effectiveness, and safety. Environmental and safety-related data is another area in which process simulators provide useful information at a lower risk and cost than real processes.
Key steps for successful business process simulation
From the flow of patients through healthcare facilities to insurance claims’ pathways through assessment, there is simply no room for errors in most industries once processes have been implemented. Weak links in any part of a process chain present new risks for lawsuits, fines, and even work stoppages.
Consequently, accurate and successful process simulations are critical for both service providers and their customers. Let’s take a look at the six steps businesses typically take, no matter the industry, to ensure process simulation success.
Step 1: Define the problem and set goals
Because every process passes through specific phases, it’s customary for teams to first develop a visual representation of it, including decision points and tasks for each of those phases.
Flowcharts and business process management (BPM) tools are great tools for visualizing every part of a process. This is called process mapping.
Once every team member can see every part of a process, they can not only detect problems and issues to be solved, but the disconnects that cause these issues. They can then set goals accordingly.
Step 2: Data collection and validation
Collect data on the process being simulated, including costs, resource availability, and task duration. This data will require validation to ensure that the model behaves realistically. Developers will then use the data to decide upon and create input parameters (value sets that allow users to input relevant data like measurement increments or dates) for the model.
This data also provides metrics that indicate the simulation’s baseline performance.
Step 3: Model development
The next step of process simulation is developing a computational or mathematical model for the process based on the process map created at the start and the data collected thus far. The model must accurately reflect the relationships between the process’s resources and tasks, and include improvements and updates based on them.
Step 4: Model calibration and verification
Run the simulation to ensure the process behaves as expected, just as if it were running in the real world. Testers should perform this step many times, adjusting the model as needed for the simulation to match the real-world process. The data produced by the simulation will change as the model is adjusted, so developers may find their areas of focus shift in this process phase as issues are resolved and new ones revealed.
Step 5: Running and analyzing the simulation
At this point, testers can simulate various scenarios with the model. This testing phase often involves developers making changes to conditions such as resource allocation, task duration, and delivery dates, to find the combination of parameters that produces the best result. In addition, testers use this step to identify problems like process inefficiencies and workflow bottlenecks.
Step 6: Scenario analysis and optimization
Finally, developers can analyze the results of the simulation to identify patterns, trends, and areas to improve. They can then adjust the process to optimize performance based on these findings, and run additional simulations to validate the proposed changes.
Business process simulation example
A manufacturing organization provides a great example of business process simulation because those types of businesses tend to run complex, well-defined processes. In this example, the company is seeking to analyze a production line to identify inefficiencies and optimize its capacity.
After laying out the entire process from end to end, company developers would create a model of the process, including its required decision points, resources, and tasks. It would then run simulations to explore different scenarios for performing the process.
In manufacturing, parameters of interest would most likely include changing the sequence of specific tasks and resource allocations. Varying these combinations might result in a new process that reduces bottlenecks or provides some other improvement over the existing process.
The results of these simulations thus provide the company with the data it needs to make an informed decision that improves the efficiency and quality of its production process.
Business process simulation and BPM
Business process simulation assesses an existing process’s overall health. It’s a method used across many industries to optimize processes, most often by removing bottlenecks.
Businesses also use simulation to implement new processes in response to a change such as a merger or new technology. Additional uses of process simulation include expanding into new markets or technical spaces by adding features to existing processes.
Pipefy’s BPM solution is a dedicated platform that creates and optimizes business process models. It features alerts and user tagging, accelerating hand-over times between process steps. Our BPM platform also provides historical data that allows you to make smarter decisions about improving your company’s processes.