ARTICLE SUMMARY
When talking about Lean, it’s inevitable that we’re going to talk about waste—after all, it’s the Lean manager’s worst nightmare. Classified as 3M, or Mura, Muri and Muda, these terms represent conditions and situations that enable the generation of waste at all levels of the organization. When identifying waste, questioning everything is an important part of the process. Think of yourself as a detective and take a closer look at all parts of your processes and all departments of your company and, once you’ve eliminated waste, it’s important to build a mindset of continuous improvement of all of your processes.
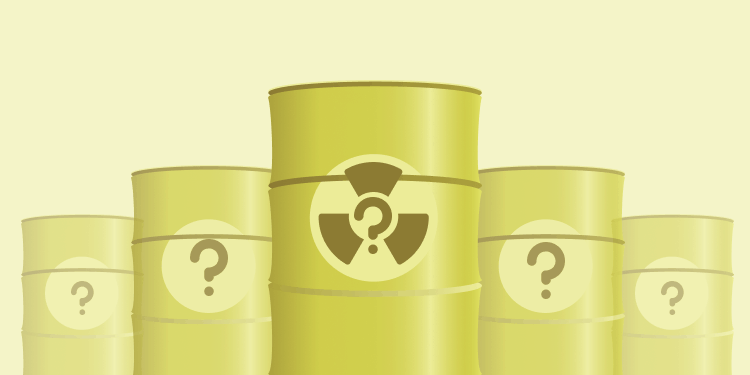
When talking about Lean, it’s inevitable that we’re going to talk about waste—after all, it’s the Lean manager’s worst nightmare. But what exactly is “waste” in Lean? How can you identify it? And most importantly—how can you eliminate it?
This content will answer you these questions and will help you understand four important Lean concepts: Waste, 3M, Continuous Improvement and Kaizen. If you want to learn the whole Lean jargon, don’t forget to check out our Lean Glossary.
The Lean Story: Who is Who in this Battle for Excellence
If you think of Lean as a classic story, the protagonist’s main goal is to achieve excellence. So these are our characters:
- Continuous Improvement: The Protagonist
- Waste: The Antagonist
- Lean Tools: The Protagonist’s Best Friend
Of course Lean has other main characters that you can meet in our Beginner’s Guide, but here we will focus on this Waste spin-off! Follow me:
Waste: The Antagonist
Your goal as a Lean manager is to achieve the best version of your work in order to deliver value to the customer and improve your results.
It may sound like a hard mission, but the rock in your way to success is simply the waste—that’s why it is the antagonist of our story. The villain. And it can be efficiently defeated by the protagonist and the best friend! But first…
How Can You Find Waste?
It comes in various forms, so it’s important to be aware of all kinds of waste and start taking a closer look at all of the processes you manage.
In Lean, waste is classified as 3M, or Mura, Muri and Muda. These terms represent conditions and situations that enable the generation of waste at all levels of the organization. Check out these practical examples:
- Any activity, machine, process or person that is not steady
- Uneven workflow for members of the same team
- High variation of demand
- Any activity, task, process or person that is overburdened
- When some of the team are otiose members, while others are overloaded with work
- When things are put off until the last minute
- Any activity, machine, process or person that is useless
- Using tools and strategies that are overhyped, even if they don’t add value to the company
- Manual work that could be done automatically
Thinking of Muda, you can go deeper and findthe seven kinds of waste in Lean:
- Transport: moving materials, documents or pieces from one place to another
- Inventory: purchasing online tools that people rarely use or more office supplies than necessary
- Motion: hosting meetings that could have been an email, badly structured workspaces
- Waiting: waiting for approval from higher management, waiting for work to arrive to you
- Overproduction: launching features nobody needed, filling in too many documents
- Overprocessing: spending too long on a given task, having multiple levels of approval for small tasks
- Rework (Defects): bugs, incorrect collection of data, and a bonus
- Skills: failing to use employees to their full potential
Note: When you have Muri and/or Mura, inevitably you have Muda, once it contemplates the seven types of waste. Here’s an example: There are weeks that you really have time on your hands. You get otiose and even have to forge activities at work—don’t lie, we know it happens to the best of us! But all of a sudden, your demand grows really fast. You don’t even have time for a coffee and some days you have to work after hours. This, my friend, is Mura! It’s the unevenness of your demand. In parallel, it generates Muda. When you’re otiose, there’s a wait for new activities—which classifies as waste number four.
ike a Detective, Investigate
When identifying waste, questioning everything is an important part of the process. Think of yourself as a detective and take a closer look at all parts of your processes and all departments of your company.
Is there rework? Is there a demand for your product or service with an acceptable rate of complaints? Are there more people than needed to get things done? Or are there fewer people than needed? What are your bottlenecks? Does the math of all your departments add up at the end of the month?
Defeating Waste
Those and several other questions will allow you to find waste and start acting on it promptly.
Now it’s where the best friend—or the Lean tools—shines. There are several options that are meant to help you on your journey. When talking specifically about waste and problem solving, these are our knights:
- VSM—Value Stream Map: It’s an effective tool to document, investigate and analyze your processes. It’s also very useful to compare your current state to your future and ideal state
- A3: As a compliment to VSM, A3 also allows you to compare present and future. It helps you understand your problems more deeply and keep track of your progression
- PDCA: This tool is all about continuous improvement. It’s a cyclical way of Planning, Doing, Checking and Acting on your problems and bottlenecks
- 5 Whys—Root Cause Analysis: As said before, there’s nothing like questioning everything. When using this tool, your goal is to find the root cause of your problems, so you can cease the problem as soon as possible. In order to do that, you question “why” until you find the answer. It usually takes five “whys”, but keep in mind that it can take more or fewer questions for each process
- Gemba Walk: The Gemba is where the magic happens, it’s where processes happen. The Gemba Walk consists of going to this magical place and observing everything with an open mind. It’s a great tool for you to spot waste and other problems that usually slip by undetected
They are complementary and easy to use. They were developed specifically to help Continuous Improvement defeat Waste.
Continuous Improvement: The Protagonist
Once you’ve eliminated waste, it’s important to build a mindset of continuous improvement of all of your processes.
Also known as Kaizen, Continuous Improvement is a culture of changing for the better in a cyclical way. In other words, it’s the practice of always finding opportunities for improvements.
Starting from that premise, Continuous Improvement is the protagonist of this story. It’s the one seeking the ultimate goal of your company: excellence. Continuous Improvement is responsible for keeping our antagonist far away from our story. It’s basically our hero!
Happily Ever After
Now, the happily ever after you seek is in your hands. Here you’ve learned more about waste and how you can identify and eliminate it successfully. You’ve learned about the ideal scenario you need to build to prevent our villain from coming back. You’ve been empowered to conquer this mission. It’s your turn now—go get’em!